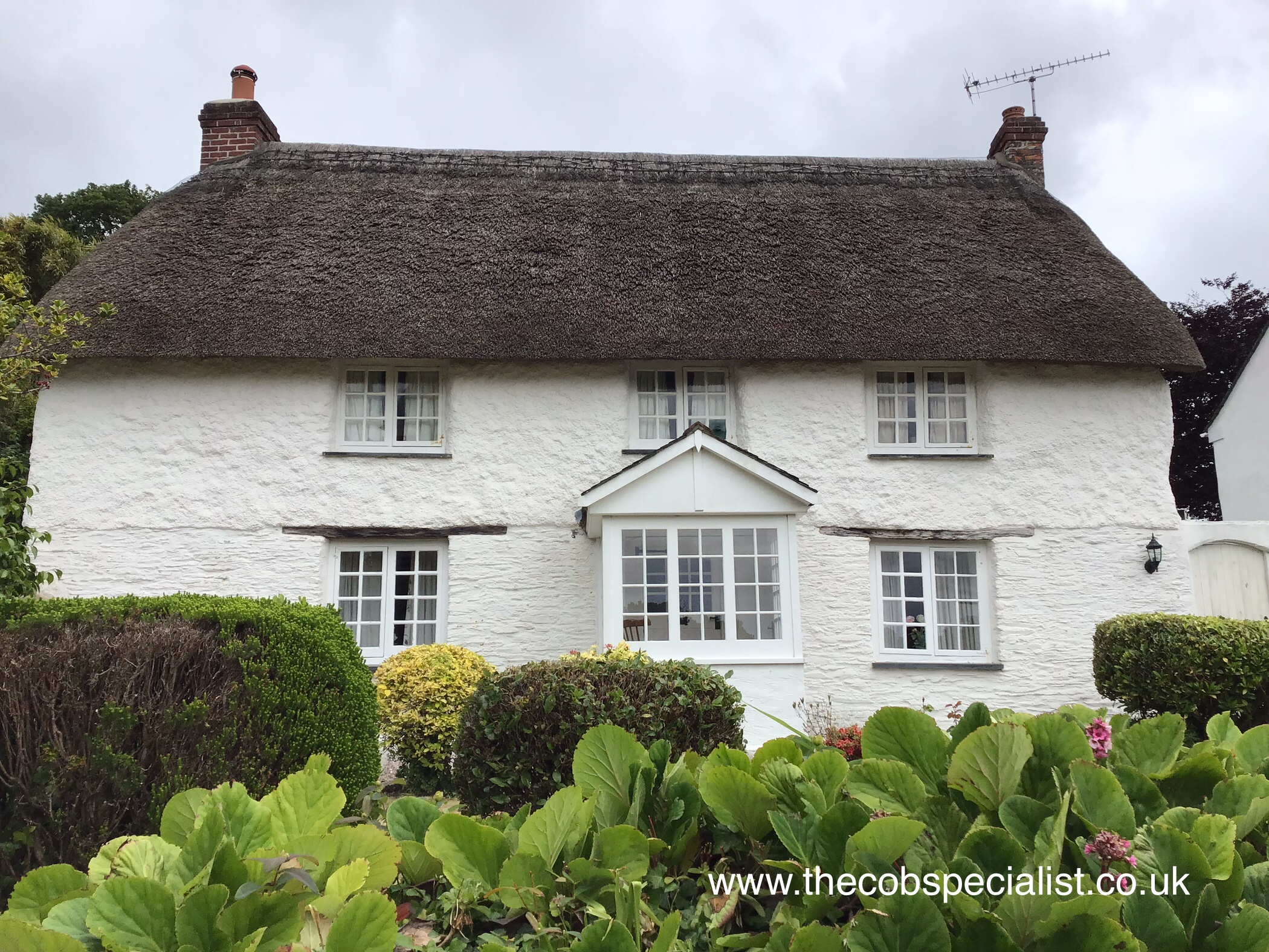
Jan
Cob Surveys – Part 1 – Where cob meets stone
Introduction
There are many building surveyors in the UK that will honestly admit to being somewhat out of their depth when it comes to surveying cob walling and cob buildings. The Cob Specialist has over 25 years experience of cob in construction…..and I’m still learning! Therefore, to expect a cob survey that delivers total accuracy and understanding from your average building surveyor can be a bit hit and miss (at best) or completely misleading (at worst). Over this coming year I am going to post a series of top tips that include – what to look for, what is obvious, what isn’t obvious, what is there, what isn’t there etc – to enlighten, inform and delight (hopefully) the reader.
Part 1 – Where cob meets stonework
Typically, all monolithic cob buildings and cob walling were built off of a natural stone plinth. The purpose of the stone plinth is to ensure that the base of the cob wall isn’t in immediate contact with ground level, whereby saturation [to the cob wall base] would be likely. A frequent height for the stone plinth is 450mm – 1200mm. There are stone plinths to 1st-floor level that were common practice too, however stone plinths of in-between heights are quite rare.
Traditionally, the cob builders of olden times would have constructed cob walling to all four aspects of the building. This method ensured a continuity of building medium ie all cob. However, there are examples of where cob walling meets natural stone walls. In essence, this wasn’t favoured because newly introduced cob has an average shrinkage of 6% (laterally and vertically) over its drying period of approx 5 years. BUT, in a few instances this was practised. So, how can the cob building surveyor ascertain if the stone wall element/s of a predominantly cob building are original [to the build] or are historic replacements, and why do we need to know?
What is the significance of these two examples of ‘tapering’ stonework at gable-end junctions with cob? Well, they inform the surveyor that the principal stonework [to the end wall] was completed first, then the cob infill was introduced and finally the gable was built to its apex. We know this because when constructing mass cob there will be shrinkage during its drying period. By tapering the stonework, gravity compensates for this shrinkage.
Gable-end walling that has been rebuilt
Having established what an original (to the build) gable-end looks like, how can the cob surveyor identify a non-original gable?
Any good surveyor will look at this scene and describe the failed/failing surface coverings, cracks in the wall, evidence of damp, inefficient/non-existent rainwater goods and high[ish] ground level…..and these are accurate observations that need to be highlighted. But what else do we see? So….what I see is the obvious separation (not the difference) but the separation between the cob and the stonework. In particular, the path the separation line takes. We don’t see a separation of direct verticality and we don’t see a separation of tapered verticality…..what we can see is a random, serpentine crack and this indicates that the stonework to the gable-end was introduced after the cob was placed in situ. Therefore, originally, the gable would have been of cob construction.
Superb example of a cob wall gable
Why does the cob surveyor need to know this?
By recognising idiosyncrasies such as these, the cob surveyor can use this information to establish historic facts about the buildings’ existence. For instance, why it is in its current condition, inform with assurance any removals and/or extensions proposed, predominant weather patterns that may have caused cob failure in the first place and [on occasion] assist with more accuracy to the buildings age.
Summary
When surveying cob walls and cob buildings it is important to gather as much information as possible. Information received via owner/occupier stories can be useful but not always accurate. Therefore, cob building knowledge is a valuable tool when deciphering the current, on-going and/or potential issues with the building and going forward, allows for an informed pathway to reparation or preservation.